Vlastenectvo sovietskej priemyselnej elity bolo spojené so spoločnou zodpovednosťou za konečný výsledok
Interindustriálna interakcia vždy - tak v Ruskej ríši, ako aj v ZSSR a dnes - nepatrila k silným stránkam domáceho priemyslu. Na rozdiel od Nemecka alebo USA, kde zmluvné záväzky mali a majú nemennú a takmer posvätnú silu.
Zoberme si napríklad vzťah medzi ruskými metalurgmi a výrobcami strojov. V druhej polovici 19. storočia nové dopravné strojárne a lodenice nedostali od uralských baníkov potrebné množstvo priemyselných kovov. Ten považoval za nerentabilné vyrábať veľa relatívne lacných valcovaných výrobkov, pretože rovnaký zisk poskytoval oveľa menší objem drahej strešnej krytiny. Chýbajúci kov na nápravy automobilov, hriadele motora a kožu lode bolo potrebné kúpiť v zahraničí. Až do konca storočia problém vyriešili juhoruské hutnícke závody založené belgickými alebo francúzskymi priemyselníkmi. Na Urale Francúzi postavili aj jeden závod - Chusovskaja.
Zdá sa, že v sovietskych časoch také výstrelky neprichádzali do úvahy. Hutnícke závody postavené v 30. rokoch navyše poskytovali krajine kov ako celok. Zakaždým, keď výrobcovia strojov požadovali nové komplexné typy valcovaných výrobkov, hutníci ich ovládali roky alebo dokonca desaťročia.
Rezortný feudalizmus
Vráťme sa k histórii Uralvagonzavodu. Už vo svojich prvých projektoch sa plánovalo použitie masívnych valcovaných oceľových kolies pod štvornápravové automobily, pretože konštrukčná kapacita dosiahla svoju konštrukčnú kapacitu, ktorej dodávateľ bol plánovaný do neďalekého hutníckeho závodu Novo-Tagil. Ten však stavalo hutnícke oddelenie a stavbu kolesovej valcovne posunulo na roky 1938-1942, a nie na prvé miesto. V dôsledku toho sa prípad nezačal pred vojnou. A po vojne sa prenájom kolies o hutníkov príliš nezaujímal. Výsledok: až do polovice 50. rokov autá Tagil odchádzali z továrne na krátkodobé liatinové kolesá namiesto oceľových. To železničiarom prinieslo obrovské straty, ale nebolo na výber: buď také autá, alebo žiadne.
To isté sa stalo so zavedením nízkolegovaných ocelí do konštrukcie vozňov. Sľubovali citeľné zníženie vlastnej hmotnosti vozového parku pri zachovaní všetkých výkonnostných charakteristík. Konštruktéri z Uralvagonzavodu začali s navrhovaním automobilov z nízkolegovaných kovov koncom 30. rokov, ale ich sériová výroba sa začala až v druhej polovici 50. rokov, pretože hutníci neposkytovali ani vhodné valcované výrobky, ani ferozliatiny na odlievanie dielov.
Treba povedať, že vírus rezortného feudalizmu zasiahol samotných výrobcov strojov. V lete 1937 sa odohral zaujímavý príbeh, ktorý charakterizoval vtedajšie medziagentúrne vzťahy. Hlavné riaditeľstvo hutníckych podnikov poslalo do Uralvagonzavodu objednávku na päťtisíc ton prírezov pre nedávno spustený obväzový mlyn závodu Novo-Tagil. Hlavné riaditeľstvo dopravného inžinierstva bolo pobúrené zásahom do podriadeného podniku. Zástupca náčelníka hlavného riaditeľstva G. G.11. júla Aleksandrov poslal list spoločnostiam GUMP a Uralvagonzavod s nasledujúcim vyhlásením: „Sme veľmi prekvapení, že riešenie takej dôležitej otázky, ako je zorganizovanie výroby obväzu na obväz v Uralvagonzavode, sa uskutočnilo bez našej účasti, a ešte viac. - nebola nám zaslaná ani kópia oblečenia odoslaného do Uralvagonzavodu … Žiadam vás, aby ste stanovili pevný postup pre zasielanie zásielok do našich tovární iba po dohode s nami a prostredníctvom spoločnosti Glavtransmash. “
V dôsledku toho bola metalurgom odopretá obväzová oceľ, údajne kvôli technickej nemožnosti odlievania vysoko kvalitných ingotov v obchode s kozubom v Uralvagonzavode. Medzitým, už v roku 1936, tu bol odliaty axiálny polotovar a v roku 1937 ingoty na valcovanie plechov. Preto ingoty pre krycí mlyn, nachádzajúce sa niekoľko kilometrov od UVZ, museli byť prevezené z závodov Vyksa a Kuznetsk. Ich kvalita bola navyše veľmi žiadúca a objem dodávok bol nedostatočný.
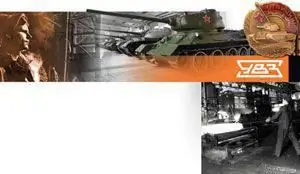
V roku 1938 sa história opakovala. Hlavným spotrebiteľom ingotov UVZ bol delostrelecký závod Molotov (tj. Perm), ktorý ku koncu roka dostal dávku slepých nábojov. A len malý počet z nich išiel do obväzu, ktorý opäť potreboval doviezť chýbajúci kov na dva alebo dva a pol tisíc kilometrov. Priemyselné záujmy v distribúcii uralvagonzavodskej ocele jednoznačne prevládali.
Rezortné choroby nešetrili ani obranný priemysel. Početné publikácie o histórii sovietskeho stavania tankov sú úplne preplnené príkladmi, ako sa stavba prototypov alebo nasadenie sériovej výroby oneskorilo z dôvodu nedodania kovu, najmä brnenia.
A ani dnes sektorový vlastný záujem nikam neodišiel, zmenil iba svoju formu. Žiadosti o nové tvary valcovaných výrobkov sa jednoducho bojujú s premrštenými cenami. O koordinovanej politike nie je potrebné hovoriť. Po páde kurzu rubľa na prelome rokov 2014 - 2015 zvýšili hutnícke spoločnosti ceny železničných koľajových vozidiel o 30 - 60 percent. A okamžite sa začali sťažovať na výrobcov strojov pre zariadenia, ktoré zdraželi - stroje sa koniec koncov vyrábajú v Rusku a nie sú viazané na výmenný kurz dolára.
Zdá sa, že v našej krajine existuje len jeden liek na medzisektorové problémy: vytvorenie vertikálne integrovaných systémov, kde sa ruda vyťažená vlastnými silami premení najskôr na kov a potom na hotové stroje.
Vojnová jednota
V našej histórii je však krátke obdobie, keď záujmy priemyslu ustúpili do pozadia. Hovoríme o Veľkej vlasteneckej vojne. Vtedajší nepochybný patriotizmus sovietskej priemyselnej elity bol spojený so spoločnou zodpovednosťou všetkých, ktorí sa podieľajú na obrannej výrobe, za konečný výsledok. To znamená, že riaditeľ obrnenej valcovne nezodpovedal ani tak za objem tavenej a valcovanej ocele, ale za počet vyrobených tankov.
Hlavný krok v tomto smere urobil riaditeľ NII-48 A. S. Zavyalov. V prvých dňoch vojny sa obrátil na vládu s návrhom, aby inštitút nariadil inštitútu zaviesť technológie na výrobu špeciálnych ocelí a pancierových štruktúr v podnikoch na východe krajiny, ktoré sa najskôr podieľali na výrobe obrneného zariadenia. vozidiel. Začiatkom júla viedli tímy špecialistov z NII-48 technologickú reštrukturalizáciu 14 najväčších podnikov. Medzi nimi boli hutnícke závody Magnitogorsk a Kuznetsk, hutnícke závody Novo-Tagil a Chusovka, závod na výrobu ťažkých strojov Ural, Gorky Krasnoye Sormovo, traktor Stalingrad, Stalingradský červený október a číslo 264. Zavyalov teda porušil predvojnové tabu: zoznam zahŕňal podniky troch ľudových komisariátov.
Vlastenectvo a povinné potláčanie rezortného egoizmu poskytovalo sovietskej metalurgii bezprecedentné tempo vývoja obranných produktov, a to ani v predvojnovom, ani v povojnovom období. V priebehu niekoľkých mesiacov bola na východe krajiny (predovšetkým na Urale) zorganizovaná výroba feromangánu, ferosilikónu, ferrochrómu, ferovanádu a ďalších zliatin, bez ktorých nie je možné získať pancierovú oceľ. Po strate západných oblastí zostal Čeľabinsk jediným závodom na výrobu ferozliatiny v ZSSR. Na ňom sa v krátkom čase tavenie zvýšilo o dva a pol krát. Vyrobilo sa 25 druhov výrobkov, ale predovšetkým išlo o rôzne druhy ferrochrómu. Tavenie feromangánu bolo založené vo vysokých peciach, a to nielen v nízko tonážnych starých vysokých peciach závodov Nižnij Tagil a Kušvinskij, ale aj vo veľkej modernej peci Magnitogorsk Combine. Na rozdiel od všetkých predvojnových myšlienok ferochróm tavili v druhej polovici roku 1941 vo svojich vysokých peciach metalurgovia závodov Nižný Tagil a Serov a vedci z uralskej pobočky Akadémie vied ZSSR poskytli veľkú pomoc pri vytváraní nového technológie. Neskôr bolo v serovských vysokých peciach zvládnuté tavenie ferosilikónu.
Na Urale ani na západnej Sibíri pred vojnou neboli žiadne obrnené tábory, museli byť narýchlo premiestnené z podnikov, ktoré boli v bojovej zóne.
V lete 1941 bolo evakuované zariadenie stále v tranzite. A potom hlavný mechanik Magnitogorsk Combine N. A. Ryzhenko navrhol valenie brnenia na rozkvitnutom mlyne. Napriek veľkému riziku sa myšlienka zrealizovala. A v októbri vstúpil do služby obrnený tábor vytiahnutý zo závodu v Mariupole. Bol zostavený za pouhých 54 dní. Podľa predvojnových štandardov to trvalo rok.
Závod Novo-Tagil získal tábor z Leningradu. Prípravy na jeho prijatie sa začali v júli, pôvodne sa predpokladalo, že bude namontovaný na mieste obväzu. Tábor obväzov bol rozobraný, ale ukázalo sa, že staré zásoby nestačili na inštaláciu obrneného tábora a museli byť umiestnené inde. Vojna prinútila urobiť to, čo sa donedávna považovalo za nemožné: len pred rokom mali pokusy o realizáciu priemyselnej výstavby integrovanou „vysokorýchlostnou“metódou v Nižnom Tagile prinajlepšom čiastočný úspech a v lete 1941 najviac komplexná stavebná operácia bola takmer dokonalá. 10. septembra bol valcovaný prvý oceľový plech Tagil mesiac pred plánovaným termínom. Celkovo bolo do konca roka získaných 13 650 ton plechu, vrátane asi 60 percent panciera (mlyn bol testovaný na uhlíkovej oceli a v októbri - decembri sa valcovala uhlíková oceľ s nedostatkom pancierov). Výsledkom bolo, že už v januári 1942 mesačná výroba pancierových platní v uralských továrňach presiahla šesť mesiacov v celom predvojnovom Sovietskom zväze.
Nemenej prekvapujúce udalosti sa odohrali aj v iných málo známych podnikoch. Počas vojny bol hutnícky závod Zlatoust objemom taviacej a valcovanej ocele nižší ako Magnitogorsk Combine, ale v sortimente výrobkov ho výrazne prevyšoval - vyrobilo sa tu asi 300 tried legovanej a uhlíkovej ocele. Bez dodávok od Zlatoustu by sa zastavila výroba mnohých typov zbraní, predovšetkým tankových motorov.
Staré uralské továrne sa ukázali ako nevyhnutné pri výrobe malých sérií obzvlášť kvalitnej ocele. Do každého sovietskeho tanku bol napríklad investovaný kov zo spoločnosti Serov Metallurgical, hlavného výrobcu kalibrovaných valcovaných výrobkov. Závod v Nizhnesalde prešiel na tavenie niklu a železa. V tomto zozname je možné pokračovať donekonečna - počas vojnových rokov, kdekoľvek bola aspoň jedna kupola, bol roztavený kov zbraní.
Existuje kuriózny príbeh s tavidlami na automatické zváranie. Pred a na začiatku vojny boli tavené v jednom z podnikov Donbassu, po obsadení ktorého sa centralizované dodávky úplne zastavili. Koncom roku 1941 začali pracovníci Ústavu elektrického zvárania Akadémie vied Ukrajinskej SSR vo viac -menej použiteľnom stave hľadať náhradné materiály dostupné na Urale. A našli ich - vo forme vysokopecných trosiek hutníckeho závodu Ashinskiy. Vyžadovali sa iba malé vylepšenia: vysoké pece obohatili ich trosky o mangán a tým ich zmenili na úplne vhodný tok. Zariadenie potrebné na testovanie bolo privezené z Nižného Tagilu priamo do Ashy.
Príklady miestnej spolupráce medzi tankermi a hutnými závodmi sú veľmi orientačné. Pred spustením vlastných zariadení bolo v hutnom závode Nižný Tagil vykonané tepelné spracovanie častí nádrží tankového závodu Ural č. 183.
Úspešnú prácu zlievarenských robotníkov UTZ výrazne uľahčila pomoc susedného šamotového závodu Nizhniy Tagil, ktorý zaviedol výrobu vysokokvalitných žiaruvzdorných zarážkových kamienkov. To umožnilo vykonávať bezproblémové odlievanie ťažkých pancierových ocelí na tvarované odlievanie.
V rokoch 1942-1945 fungovali otvorené pece v UTZ predovšetkým na koksárenskom a vysokopecnom plyne z koksárenských závodov Novo-Tagil a Nizhniy Tagil. Plynovod je v prevádzke od februára 1942. Vlastná stanica na výrobu plynu č. 183 neposkytovala viac ako 40 percent potrieb.
Niekedy na vyriešenie problému stačila jednoduchá rada. Informácie od miestnych hutníkov o malej mangánovej bani vyvinutej v 70. rokoch 19. storočia pomohli prežiť niekoľko týždňov pred začiatkom dodávok feromangánu bez zastavenia odlievania tankových tratí.
Ďalší príklad: Ako sa zvyšovala výroba pancierovej ocele, obchod s otvoreným kozubom už nedokázal držať krok s tavením kovu pre hlavy leteckých bômb. Zvonku to nebolo možné získať. Riaditeľ Ju. E. Maksarev vo svojich spomienkach pripomenul priebeh ďalších udalostí: „Keď som bol na jednom zo zasadnutí v mestskom výbore, stretol som sa s riaditeľom starého, ešte stále demidovského závodu, a požiadal som, aby odo mňa vzal odliatok hlavy bômb. Povedal: Nemôžem pomôcť s oceľou, ale s radou pomôžem. A keď som prišiel do jeho závodu, ukázal mi jeden a pol tonový prevodník Bessemer so stredným fúkaním. Dal mi výkresy a povedal, že vie, že máme dobrú zlieváreň mechanizovaného železa a vaše konvertory budú zvárať “. Takto sa objavila objednávka závodu z 8. septembra 1942 na organizácii v obchode s kolesami Griffin v sekcii Bessemer troch malých prevodníkov (po jednom a pol tony kovu). Do 25. septembra projekt pripravilo konštrukčné a technologické oddelenie riadenia investičnej výstavby, špecialisti odboru hlavného mechanika rýchlo zvarili meniče a kotly - skladovacie nádrže na tekuté železo. Skúšobná prevádzka oddelenia Bessemer a odliatie experimentálnej šarže piatich názvov dielov sa uskutočnili na prelome októbra a novembra 1942. Sériová výroba sa začala koncom novembra.
Na konci témy: Spolupráca hutníkov a staviteľov nádrží za vojny pôsobila v oboch smeroch. Inštalátori tankového závodu Ural sa zúčastnili uvedenia do prevádzky mnohých nových blokov hutníckeho závodu Novo-Tagil. V máji 1944 bol v odlievárni obrnenej veže vyrobený značný počet obkladových dosiek na opravu vysokej pece.
Ale hlavným asistentom metalurgov bol samozrejme závod na výrobu ťažkých strojov Ural. Knihy objednávok pre UZTM na roky 1942-1945 sú doslova preplnené dokumentmi o výrobe náhradných dielov a zariadení na metalurgické účely - pre potreby tankového priemyslu aj pre podniky Ľudového komisariátu železnej metalurgie. Na jeseň 1942 bola v UZTM oficiálne obnovená špeciálna divízia na výrobu zariadení pre hutnícke závody. Dostal kód „Divízia 15“a bol podriadený zástupcovi riaditeľa pre nákupy a výrobu trupu.
Úspech na priesečníku odvetví
Spolupráca hutníkov a staviteľov nádrží viedla k vytvoreniu množstva technológií, ktoré bez preháňania možno nazvať skutočnými vedeckými a technickými prelommi.
Po roztavení a valcovaní pancierovej ocele na plechy hutníci presunuli svoje výrobky do výroby pancierového trupu. Tu bol kov rozrezaný podľa šablóny na zodpovedajúce časti. Pri výrobe „tridsiatich štyroch“obzvlášť veľa problémov spôsobili dve časti trupu: blatníky (šikmá strana boku) a zvislá bočná doska. Oba boli dlhé, dokonca aj v šírkových pásoch so šikmými rezmi pozdĺž okrajov.
Myšlienka sa prirodzene navrhla navinúť merací prúžok rovnako široký ako hotové diely. Prvýkrát ho formulovali obrnené autá závodu Mariupol v lete 1941. Na skúšobné valcovanie sme vybrali brúsku v Zaporizhstale, kam boli odoslané dve poschodia pancierových ingotov. Potom však nemali čas začať podnikať: postupujúce nemecké jednotky zajali echelóny aj samotné Záporožie.
Na prelome rokov 1941-1942, počas evakuácie a rozvoja výroby brnení v nových továrňach, nebol dostatok pruhov. V máji 1942 však Ľudový komisariát železnej metalurgie opäť dostal príkaz na jeho prenájom pre tanky T-34 a KV. Úloha sa ukázala byť ťažká: tolerancie na šírku by nemali presiahnuť -2/ + 5 milimetrov, tvar polmesiaca (ohyb) pre celkovú dĺžku časti bol 5 milimetrov. Praskliny, západy slnka a delaminácia neboli povolené na okrajoch, aby bolo možné zváranie vykonávať bez obrábania alebo rezania plameňom.
Experimentálne práce sa začali súčasne vo valcovniach hutníckych závodov Magnitogorsk a Kuznetsk, najskôr bez akýchkoľvek konkrétnych úspechov. Prenájom dielov pre tanky KV bol čoskoro opustený, ale T-34 bol nakoniec úspešný. Úplne nový tím autorov pozostávajúci z vedúceho hutníckeho oddelenia NII-48 G. A. Vinogradova, hlavného inžiniera KMK L. E. Vaisberga a inžiniera rovnakého závodu S. E. stojí „900“železničného a konštrukčného mlyna. metóda valcovania „na hrane“. V januári 1943 bolo vydaných 280 pásov, vo februári - 486, v marci - 1636 kusov. V apríli sa po všetkých požadovaných testoch začal s vývojom hrubej výroby meracích pásikov pre vložky podbehov tankov T-34. Spočiatku boli dodávané do UZTM a tankového závodu Ural a potom do iných tovární - výrobcov tankov T -34. Šrot, ktorý mal pôvodne 9,2 percenta, do októbra 1943 klesol na 2,5 percenta a z neštandardných pásikov sa vyrábali menšie diely.
Úplné a presné vyhodnotenie novej technológie je uvedené v zodpovedajúcej správe TsNII-48 z 25. decembra 1943: „Bola vyvinutá, testovaná a zavedená do hrubej výroby zásadne nová metóda valcovania širokého pancierového pásu„ na okraji “., ktorý bol donedávna považovaný za neuskutočniteľný v ZSSR a v zahraničí. Získanie kalibrovaného (meraného) pásu so šírkou hotovej časti pancierového trupu tanku T-34 umožnilo továrňam NKTP prijať novú vysokovýkonnú technológiu výroby pancierových dielov bez rezania pozdĺžnych hrán. Vďaka aplikácii novej metódy na jednu z hlavných pancierových častí tanku T-34 (blatníky) bola pri ich vyrezávaní dosiahnutá veľmi výrazná úspora času (asi 36%). Dosiahnuté úspory 8C pancierovej ocele až 15 percent a úspora kyslíka 15 000 cbm na 1 000 trupov “.
Do konca roku 1943 bolo zvinutie meracieho pásu zvládnuté pre ďalšiu časť trupu T -34 - zvislú časť boku. Zostáva len dodať, že autori tohto vynálezu boli za rok 1943 ocenení Stalinovou cenou.
V tom istom roku 1943 bol spoločným úsilím laboratória Ukrajinského ústavu kovov (pod vedením PA Aleksandrova) a pracovníkov Kuzneckej hutníckej kombinézy a tankového závodu Ural vyvinutý a osvojovaný špeciálny periodický valcovaný profil vo výrobe na obstarávanie. hmotnosti a kritických častí „tridsiatich štyroch“- osí vyvažovača. Prvá experimentálna dávka periodického profilu bola prijatá na KMK v decembri, začiatkom roku 1944 sa začala sériová výroba. Do októbra nádrž v Uralu úplne prešla na výrobu vyvažovacích náprav z nového polotovaru, ku koncu roka sa k nemu pridal UZTM. V dôsledku toho sa produktivita kovacích kladív zvýšila o 63 percent a počet zlomení dielov klesol.
Úspešnú prácu staviteľom nádrží výrazne uľahčili koľajové vozidlá bandážneho mlyna hutníckeho závodu Novo-Tagil. Počnúc jarou 1942 dodávali valcované ramenné popruhy so zníženými príplatkami za obrábanie, v roku 1943 boli príplatky opäť znížené. V kombinácii s novým rezacím nástrojom to umožnilo vykonávať časovo náročné odoberanie ramenných popruhov striktne podľa plánu a bez veľkého stresu. Vzácny prípad: ľudový komisár tankového priemyslu V. A. Malyshev vo svojom rozkaze z 28. septembra 1943 považoval za potrebné vyjadriť osobitnú vďaku metalurgom Tagil.
A nakoniec posledný príklad: v roku 1943 sa ráfiky podporných tankov T-34, najskôr v závode Čeľabinsk Kirov a potom v iných podnikoch, začali vyrábať zo špeciálnych profilovaných valcovaných výrobkov. Tento úspech bol tiež zaznamenaný v poradí V. A. Malysheva.
Zostáva dodať, že špecialisti americkej spoločnosti „Chrysler“, ktorí študovali tank T-34-85 zajatý v Kórei, obzvlášť poznamenali dokonalosť oceľových prírezov, z ktorých bolo bojové vozidlo vyrobené. A tiež skutočnosť, že často prevyšovali výrobky amerických hutníckych podnikov.